Introduction
K series automatic blow moulding machines are configured with tie bar clamping system, which distinguishes them from the U series machines. They are suitable for molds in extended vertical size. K-blow molding machine series are easy to manipulate and fix up. It can also be equipped with parison control system and auto deflesher system according to practical applications. This machine is characteristic of less consumption of energy, material and labor, while of high production rate. In K-automatic blow moulding machines, all components are produced by CNC machines in order to maintain high precision.
Features
- 1. Average energy consumption is 10% to 15% lower than that of homogeneous products in market.
- 2. K-automatic blow moulding machines can be remotely controlled through WIFI or 3G.
- 3. It features high automation.
- 4. Advanced CNC technology components are utilized to produce high-precision machine components.
Products by K Series Automatic Blow Moulding Machines
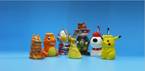
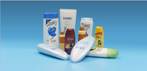
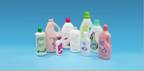
Technique Features of K-Blow Molding Machine Series
- 1.Tie Bar Clamping System
- In K series automatic blow moulding machines, the direct-acting clamping system transfers the force directly to the middle of the back platen and converts the same force to the front by four tie bars and an alignment rod. It also comes with a unique way of re-adjusting the deflection as well as the platen parallelism. Besides, the top and side opening design also offers fast mould change.
- 2. Single and Multiple Extrusion Heads
- The single and multiple extrusion heads are available with side feed and center feed designs. In the automatic blow moulding machines, each head is a single head fitted to a manifold that splits the stream of melt into the appropriate number of channels. The quantity of flow in each channel is controlled by an adjusting screw. A view stripe option is available for all head sizes in single or multiple executions. All heads in K-blow molding machine series can be optionally equipped with an electronically controlled parison thickness programmer.
- 3. CO-EXTRUTION HEADS
- Co-extrusion heads in Leshan automatic blow moulding machines are compact, reliable and with excellent functions. As the most critical part for production of multi-layer containers, they are featured with accurate control of material distribution and layer thickness. These heads can form six-layer articles at most.
- 4. AUTOMATIC FINISHING
- For post-cooling, it allows a significant increase of productivity by cooling the products in a mask before the de-flashing process. For auto-deflashing, Leshan applies three types of de-flashing systems in the automatic blow moulding machines: in-line hydraulic/pneumatic punching, in-line rotary cutting and outside stand alone deflashing unit (puncher or rotary cutter). All processes can be finished within the moulding area.
- 5. EXTRUDER
- (1) Extruder drives of K-blow molding machine series are available with a hydraulic motor or inverter-controlled electric motor. The screw speed can be adjusted smoothly from the front operating panel. In K series automatic blow moulding machines, each heating zone of the extruder is controlled individually and is usually supplied with a cooling fan to steadily control the heating parameters.
- (2) The grooved barrel fulfills that little friction generates when materials are mixed. Hence, the extruder subjects to less wear and tear.
- 6. HYDRAULIC SYSTEM
- Hydraulic components of our automatic blow moulding machines are supplied mainly by the world famous brands: Bosch Rexroth, Yuken, etc. LESHAN have joined hands with these suppliers in developing a new cost-efficient hydraulic system. Also, worldwide support from these suppliers serves well to the benefit of our users around the world to get the fastest possible response regarding spare parts and service.
Attention
When the automatic blow moulding machines are running, following requirements should be fulfilled: stable blowing air, low temperature cooling water and continuous electricity supply.